Our products have been chosen by a number of original equipment manufacturers across the country and abroad. We are chosen as a preferred composite parts supplier by a number of OEMs thanks to our proven track record of commitment to long-term vendor agreements.
When it comes to supplying composite parts to such strategic sectors as wastewater treatment, mass transit, electrical industry and military, it is often critical to have the entire process, from concept development to full production, handled by one single supplier. An approach like this ensures the consistency of the process, from the first steps of design, throughout the entire production cycle to the final product assembly.
That’s why Protectolite™ has expanded to become a one-stop shop for composite services to our customers. From concept development, design, prototyping, testing, tooling design & manufacturing to full production, Protectolite™ is your ultimate destination for all your composite needs.
With representatives throughout the USA and Canada, we are able to meet the demands of our customers no matter where they are located. With our well-planned logistics system and regularly replenished materials inventory, we can supply parts to the manufacturers with daily/year-round production across all of North America. We ship to a dozen plus OEM locations across the US and Canada every day, ensuring timely and safe delivery of our products with every shipment.
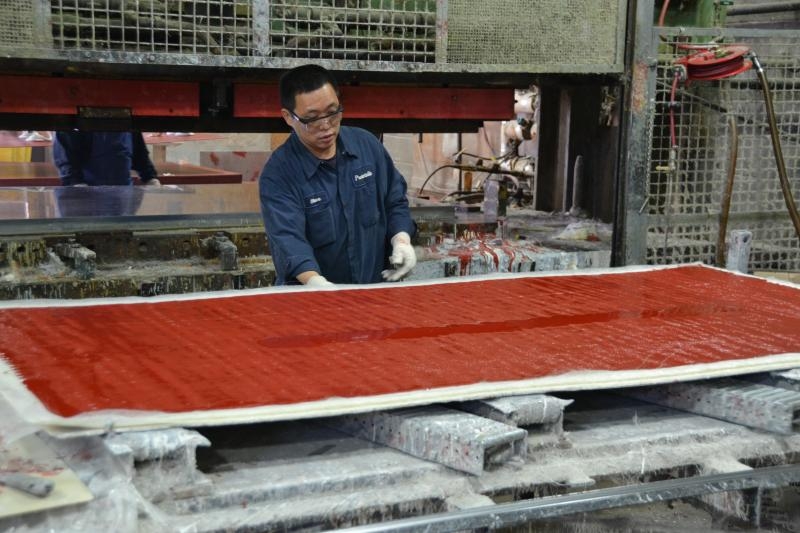
Our engineering and manufacturing capabilities combined under one roof allow us to offer complete composite solutions to meet the needs even of the most demanding industries.
Protectolite™ boasts a 35000 square foot manufacturing facility equipped with the latest technology and machinery such as twelve hydraulic presses with 75 to 1500 tons of force. Our 6-axis robotic routers and cutters as well as 3-axis waterjet table allows us to cut products of virtually any shape and size. Our customers can choose from a variety of molding materials and processes to get the product that is customized for their application.
Our molding materials selection includes:
SMC - Sheet Molding Compound:
- Combines the ability to control resin input with medium length fibers
- Excellent for larger components that require highly refined surface finish, design complexity, and good mechanical properties.
BMC - Bulk Molding Compound:
- Clay-like substance that is a mixture of resins, additives & short fibers
- Perfect for smaller sized customized components where SMC fibers are too long or where elevated loadings of flame retardants are required for optimal electrical performance.
Wet Mat / preform:
- Mat made of a combination of continuous glass fiber and/or random strands, with the option to add a binder for shaped rigidity
- Excellent for products requiring medium to large parts with a high concentration of fibers and consistent cross-sections.
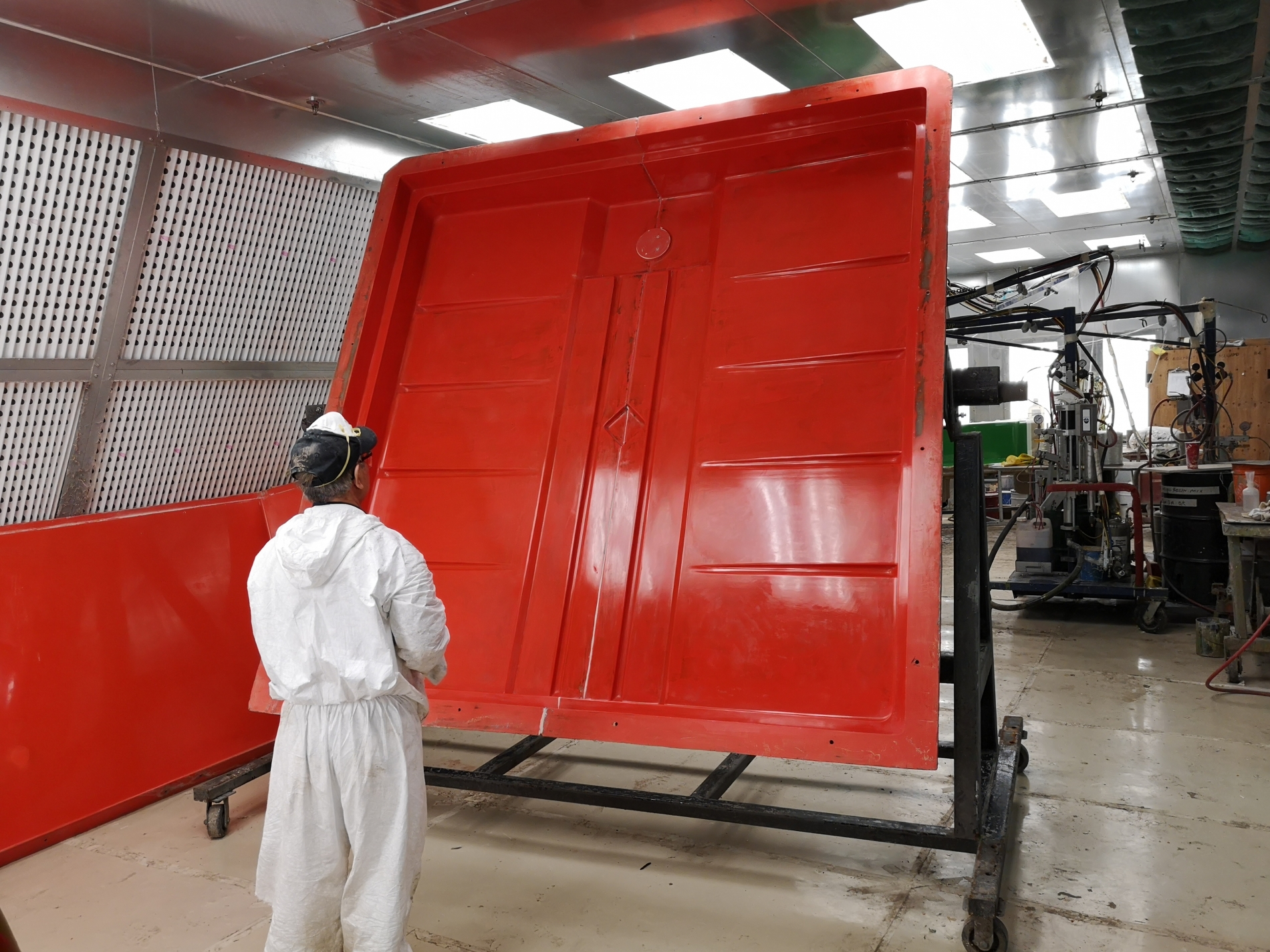
SMC - Sheet Molding Compound:
- Suitable for low to medium volume production where assembly is not a key factor.
- Advantages: simple, low cost tooling, virtually no limitations to part size, short lead times to production.
Vacuum Bag Molding:
- Suitable for products requiring a medium to large surface, like truck & bus body side parts.
- Advantages: the length of the product is practically limitless. Higher degree of process control than found with hand lay-up.
Resin Transfer Moulding & Cold Press Moulding:
- Suitable for small and medium volume production, resin transfer moulding is best for hundreds to thousands of parts.
- Advantages: Molds are less expensive than for compression molding, and full heat is not required for resin transfer moulding. It can also provide good surface finish, and the parts are more accurate in production relative to hand lay-up & vacuum bagging.
Compression Matched Molding:
- Suitable for high strength, small, medium & large complex parts requiring good surface finish in larger quantity volumes. It is best for parts in the hundreds to thousands of parts.
- Advantages: can create relatively large single-piece products at high daily production rates. Additionally, reproducible custom coloring can be incorporated into the finished product as well as ribs, metal inserts and other time/cost saving design features. Precise tolerances, repeatedly produced in single parts. Low part cost.
Pultrusion Molding:
- Suitable for products requiring a constant cross section such as: rods, structural shapes, beams, channels, pipes, tubes. High strength is due to the high concentration and parallel orientation of the fibers to the product being drawn through the pultrusion process.
- Advantages: the length of the product is practically limitless. Precise tolerances, repeatedly produced from part to part. Low part cost.