Engineered to Order: Moulding Techniques That Meet Your Complex Demands
Our 35,000 sq. ft. manufacturing facility is equipped with powerful, cutting-edge machinery capable of performing advanced moulding methods. Combined with our decades of experience, attention to detail and passion for development, we can deliver high-quality, cost-effective solutions that are tailored to your specific needs. We guarantee precision and consistency across all production scales.
We employ the following moulding methods:
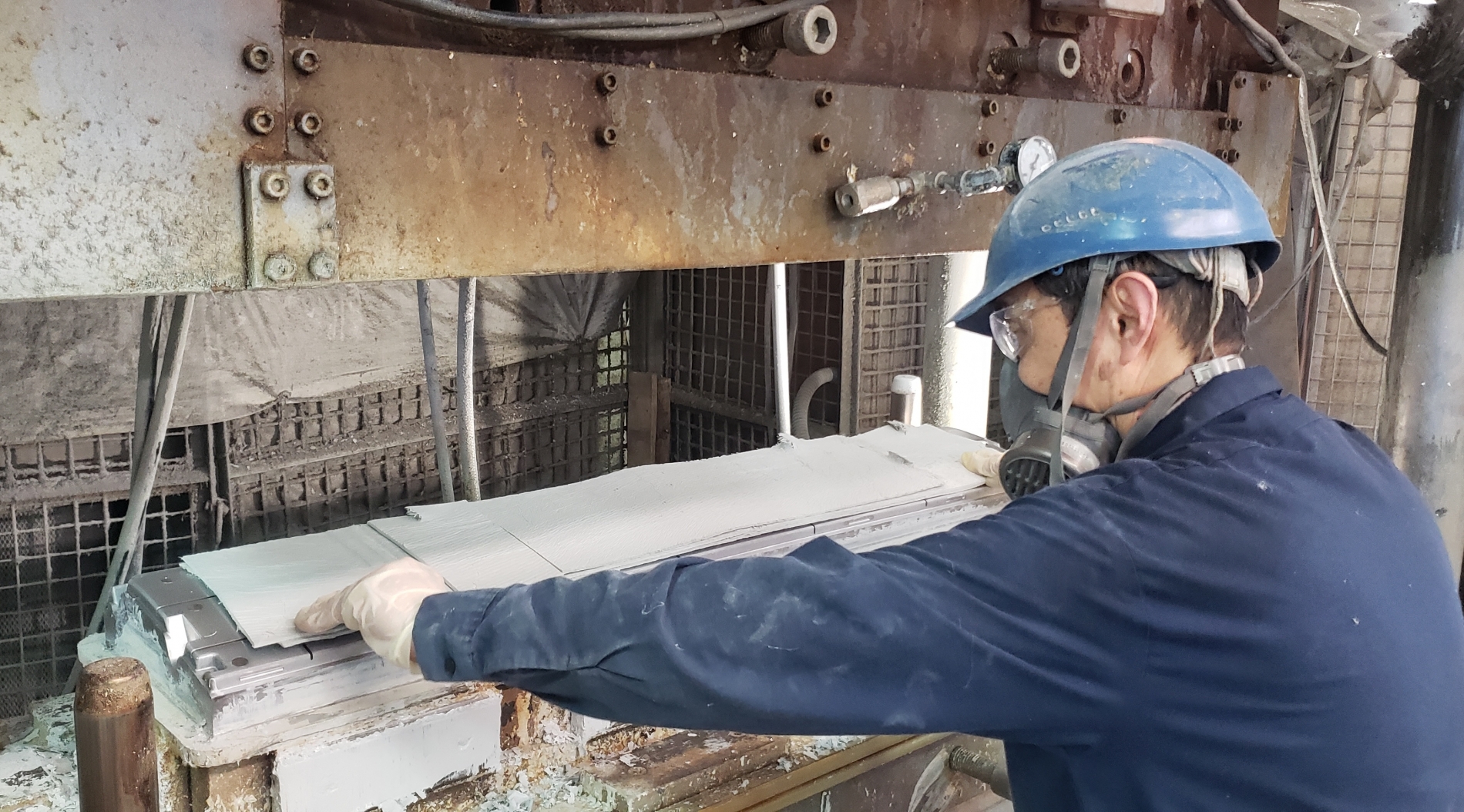
A highly efficient process, compression moulding involves the placement of composite material into a heated matched metal die mould using high pressure and heat. This production method results in parts that excel in terms of structural integrity, surface finish, part accuracy and repeatability. It is ideal for producing large volumes of uniform components that require accuracy and consistency.
Advantages:
- High volume production with precise results: Offers consistent results despite high production volumes; best suited for small to medium-sized parts.
- Large capacity with versatility: Capable of producing parts as large as 8 ft. in length and 4 ft. in width; or as small as 5 in. x 5 in. or smaller if required.
- Cost-effectiveness for large volume production: Large presses capable of handling greater production volumes, thus significantly reducing cost per unit.
- Quick turnaround: Fast and effective moulding method ensures quick turnaround-time, making it ideal for high-demand projects.
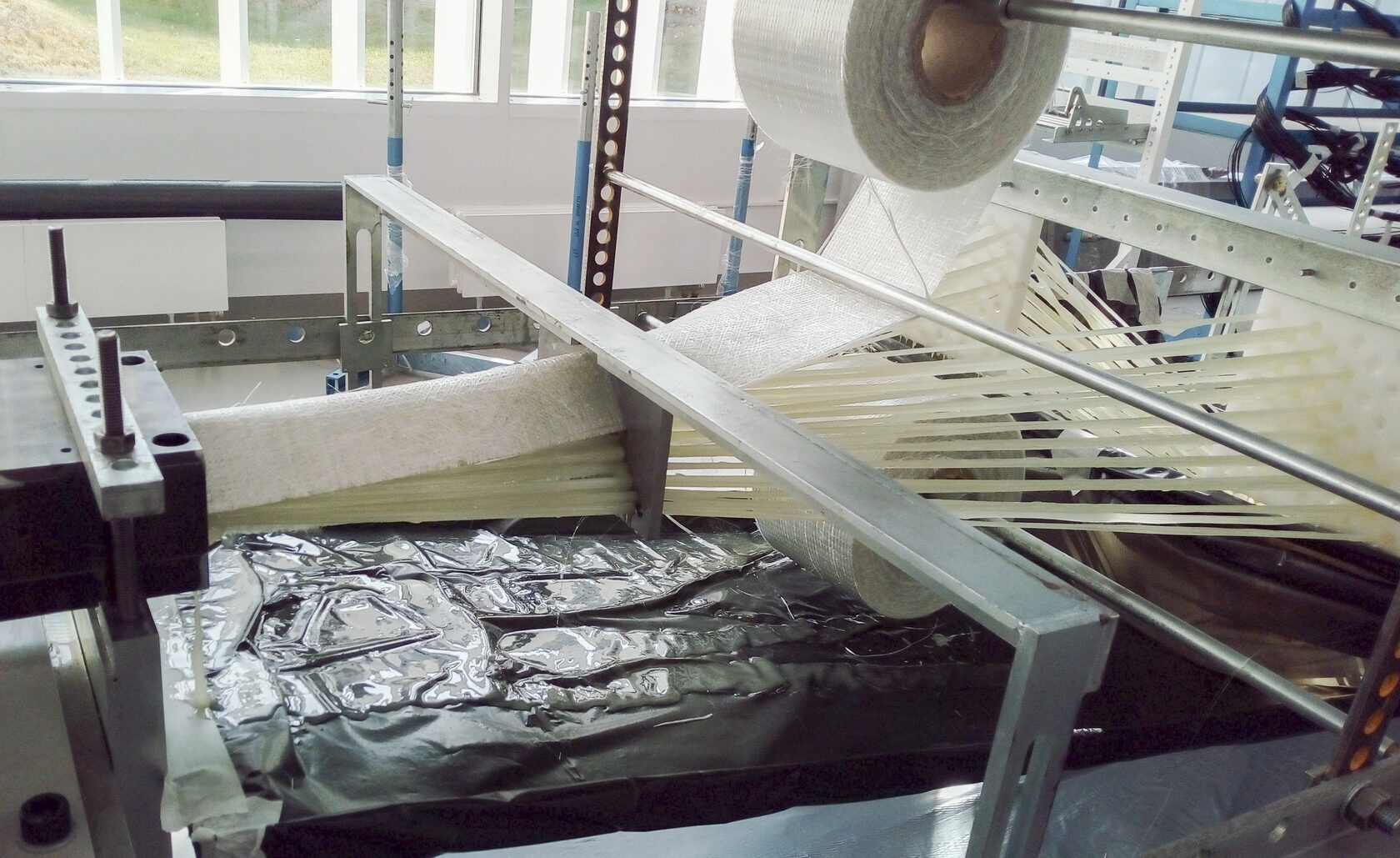
Pultrusion moulding shares similarities with compression moulding. In this continuous manufacturing process, composite materials are pulled through a heated die. This helps in creating angled parts, as well as continuous components of varying lengths. The act of pulling, as opposed to pressing, ensures uniform alignment as well as reinforcement. This results in parts that enjoy an excellent strength-to-weight ratio. Pultrusion moulding is perfect for manufacturing lightweight yet strong components of varying lengths.
Advantages:
- Versatility: Capable of producing continuous parts with long lengths and varying custom shapes such as FRP angles.
- High-quality, greater volume: Offers a high production capacity that delivers consistently high-quality results.
- Highly efficient: One of the fastest moulding methods; highly suitable for projects with demanding deadlines.
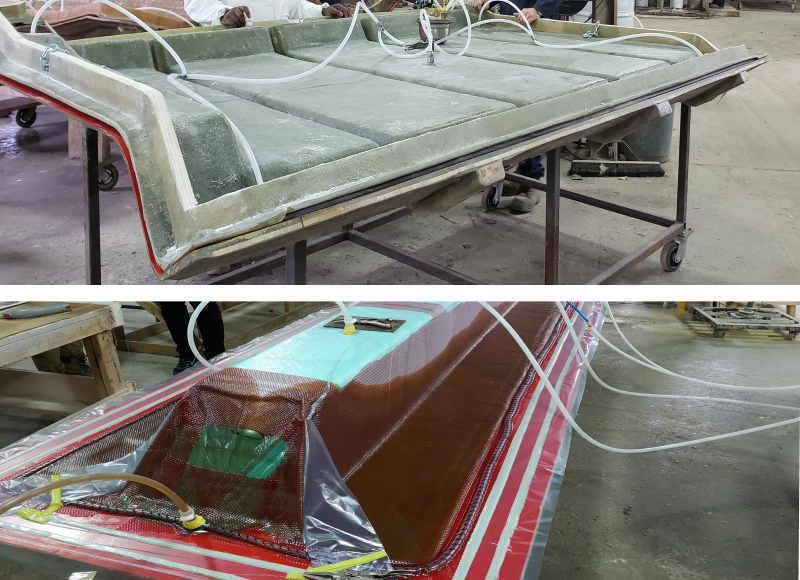
A closed-mould process, Lite-RTM involves injecting resin into the mould using a vacuum. This enables greater control over the flow of the resin, which not only reduces waste but also ensures a high level of consistency. This approach is best suited small, medium and large parts with mid-volume production runs.
Advantages:
- Higher part accuracy: Capable of handling mid-volume runs while offering consistent results and high-quality output.
- Cost effectiveness: Optimizes production costs for mid-volume orders.
- Low Capital Cost: Production of fiberglass moulds is less costly that matched-metal die moulds.
- High efficiency: Good production output and short mobilization time allows for effective production runs.
Vacuum Infusion: A semi-open moulding setup, this process involves placing the plastic bag on top of the fiberglass. Resin is infused into the laminate with the help of vacuum pressure, which ensures minimum wastage along with thorough resin distribution. The entire process is very efficient and precise.
Advantages:
- Cost-effective: Delivers high quality results while being suitable for small production runs. Lower mould capital cost compared to Compression, Pultrusion and LRTM.
- Improved fiber-to-resin ratio: Reduces wastage while ensuring integrity and strength of the finished product
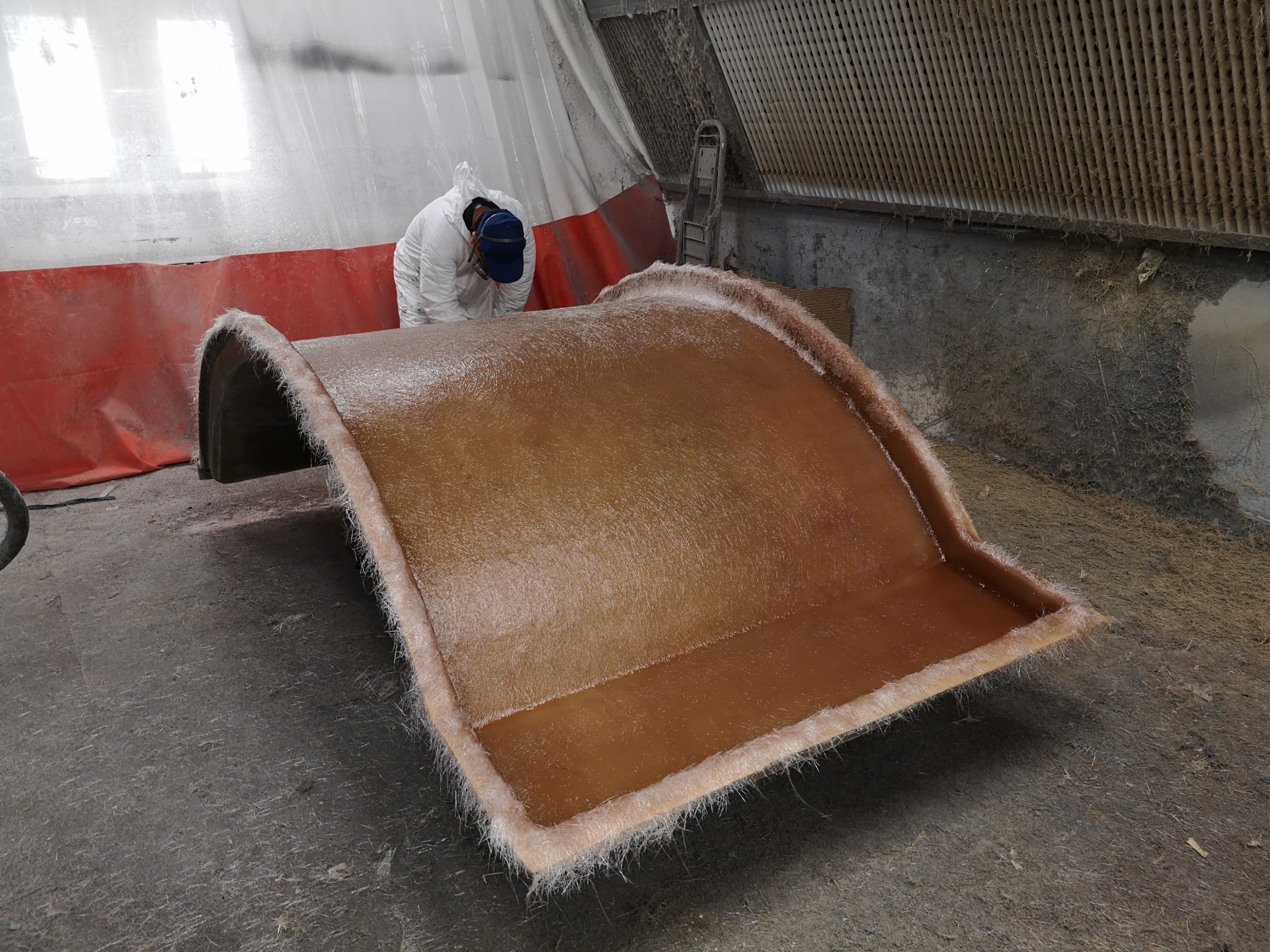
A traditional yet versatile approach to composite moulding. Flexible in nature, ideal for low-volume production runs. Hand layup centers around the manual application of resin onto reinforcement material with the help of basic tools such as brushes and rollers. Taking a hands-on approach, this method allows for quick low-cost mobilization but is highly dependent on skilled laborers.
Advantages:
- Highly affordable: A slow but cost-effective process that is the most economical choice for low-volume production runs.
- Customizable: Ideal for projects with unique specifications that are adaptive to higher degrees of variability.
- R&D: Suitable for prototyping and research projects for new ideas and parts.